Initiatives for the Next Generation
Research and Development for the Next Generation
At Nippon Soda, we see climate change as one of the key challenges facing society. As such, in addition to the supply of low-carbon products, we are also focusing our attention on hydrogen, a next-generation clean energy source that does not emit CO2 when used and that can contribute to a decarbonized society. Aiming to launch new businesses in this field, on top of internal resources, we are also making use of external collaborations with partners from industry and academia to drive research and development.
SDGs
Materiality
Achieving a low-carbon society
-
01
Contribution by supplying low-carbon products
-
02
Engaging in initiatives aimed at the hydrogen economy
KPI
① Current Initiatives
High-efficiency hydrogen generation electrode using solid-solution alloy nanoparticles
Nippon Soda and Kyoto University became the first to succeed in the synthesis of platinum-tungsten solid-solution alloy nanoparticles. When used in the electrolysis of water, this synthesis technology can generate a hydrogen evolution reaction (HER) that demonstrates the highest level of catalytic activity in the world. The technology makes use of Nippon Soda’s metal particulation and dispersion technologies. Moreover, the results of this joint industry-academia research project were published in the Journal of the American Chemical Society, and received wide acclaim from external circles. We are also researching ways to use this technology to convert carbon dioxide into valuable substances.
Introduction of continuous flow synthesis technologies
Continuous flow synthesis technologies are garnering attention for use in manufacturing methods that can contribute to the achievement of a highly energy efficient, low-carbon society. Aiming to implement these technologies, we are participating in the corporate sponsored Green Material Conversion research program led by the University of Tokyo, and are working with the university and Active Pharma to strengthen the relevant technologies.
Materiality
Forming partnerships to achieve goals that cannot be accomplished by the Nippon Soda Group alone
-
01
Sharing philosophies for the goals and cooperating with other companies and organizations
KPI
① Current Initiatives
To strengthen and expand our existing businesses, and to create new businesses, it is essential that we engage in open innovation to make use of external research resources and technologies in addition to our own. As such, we are promoting R&D through collaboration with external institutions in industrial and academic circles.
In FY 2024, we worked with 25 external research institutes (including 22 universities) to promote a range of R&D themes.
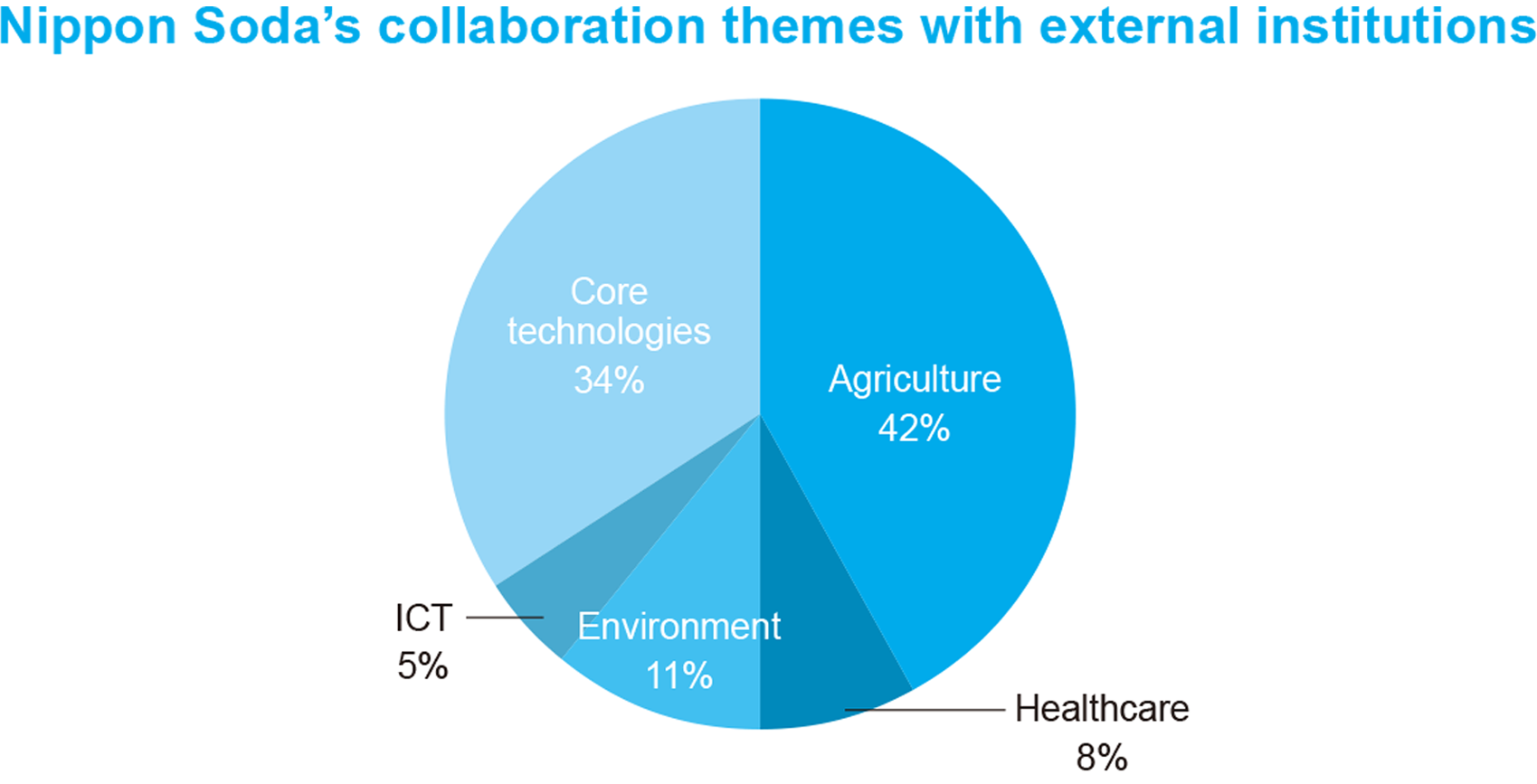
Materiality
Research and development for the next generation
-
01
Research and development that enables the continuing development of human society and the global environment, and that leads to business
KPI
① Status of Research and Development
To achieve our long-term vision Brilliance through Chemistry 2030, we are working on the development of new products and the creation of new businesses. We believe that owning high-quality intellectual property rights are essential for launching new products, increasing our market share, and entering new business domains. As such, we are actively filing patent applications for the new inventions that arise from our research and development, and building an intellectual property portfolio.
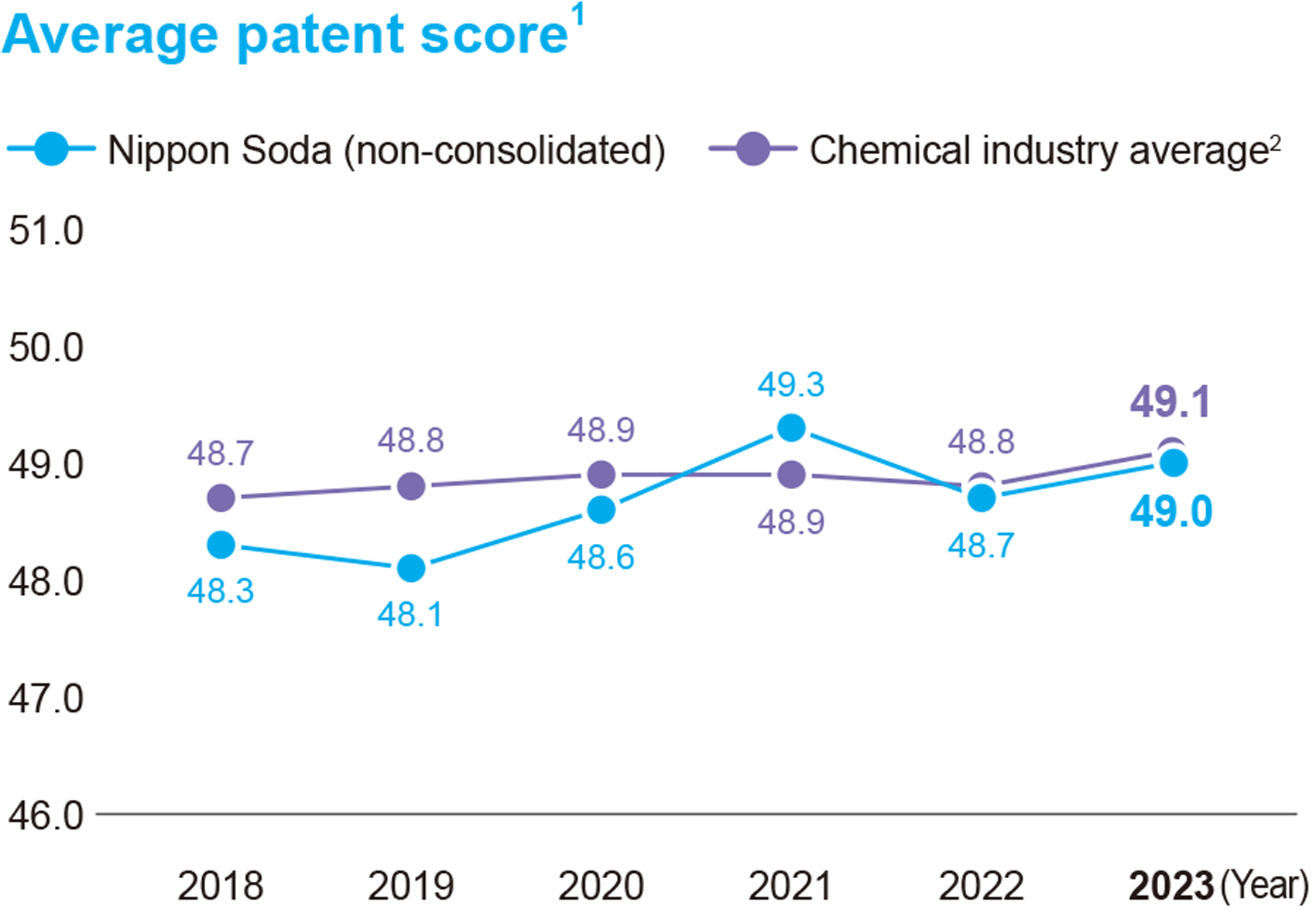
Data aggregation date: December 31 each year
- 1. Patent scores are numerical indicators of the level of attention a patent receives. The higher the patent score, the higher its market profile. Furthermore, the higher the average score of a patent portfolio, the higher the quality of said portfolio. Average patent scores have been calculated using Biz Cruncher, a program offered by Patent Result Co., Ltd.
- 2. Chemical industry averages have been calculated based on the 82 companies listed on the Tokyo Stock Exchange under the Chemicals sector (one of the 33 sectors on the TSE).
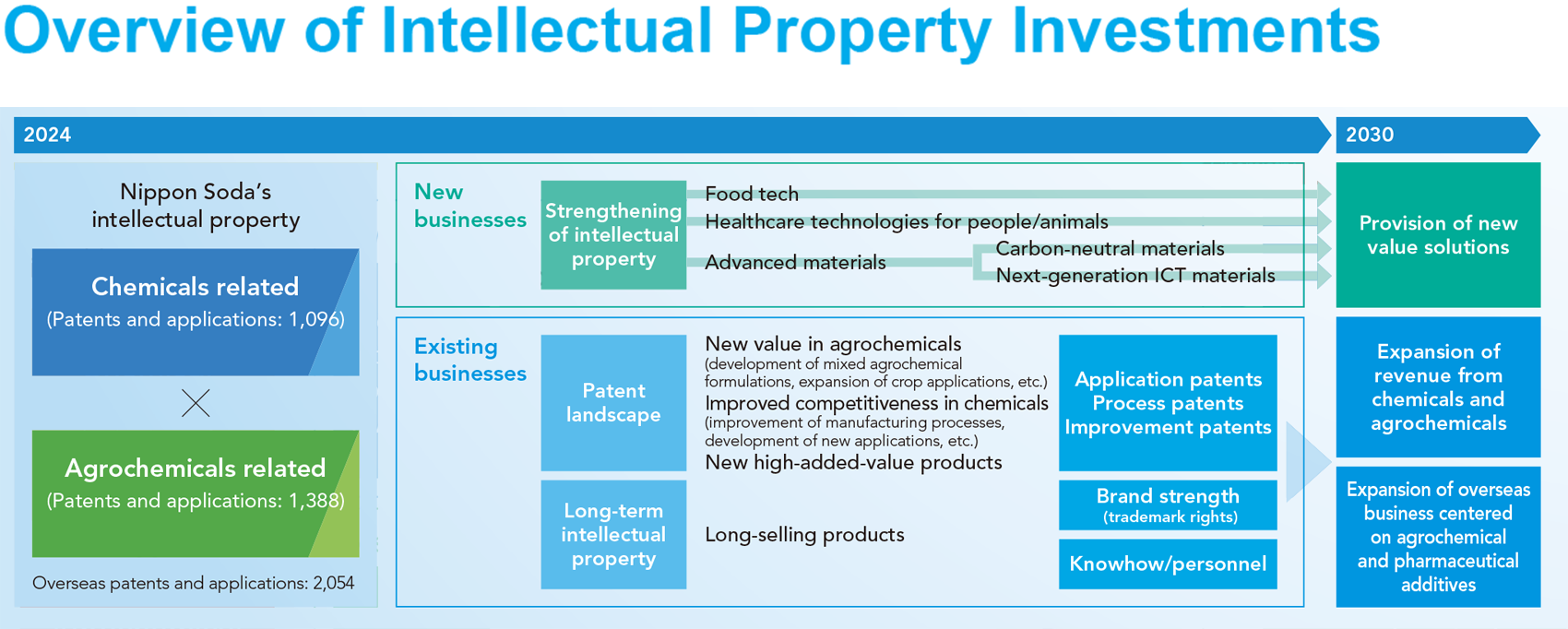
Manufacturing training programs with emphasis on experiential learning
(NTTC: Nisso Technical Training Center)
Aiming to transfer expertise and develop employees who can maintain the safety and high productivity of manufacturing workplaces, in FY 2016 we launched the Nisso Takaoka Academy at the Takaoka Plant to provide systematic training programs for newly hired manufacturing personnel. Training is mainly provided to personnel newly hired at all Group companies in Japan.
The emphasis of the training is on experiential learning. With their safety assured, participants can experience falling from a high place, encounter water and gas leaks resulting from loose bolts, and come up against other situations that they cannot experience from desk-based learning. Participants are provided with opportunities to experience simulated risks and failures that would not be possible during on-the-job training. The valuable experience they gain through these programs helps increase their awareness of the need for accuracy and safety in their work, which can then be applied to their activities in the workplace.
In FY 2020, we commenced a series of manufacturing training programs with emphasis on experiential learning. These programs were part of a two-year plan to expand educational facilities and increase equipment used for safety education. In April 2021, we established the Nisso Technical Training Center (NTTC). To further enhance safety awareness, we will provide experiential safety education to other employees in addition to newly employed manufacturing personnel.
Materiality
Developing human resources for the next generation
-
01
Educational system to foster a culture of safety for the future
KPI
① Training Initiatives
Manufacturing training programs (April 1, 2023–March 31, 2024)
- First-year training: Nihongi Plant (3 employees), Takaoka Plant (8 employees), Mizushima Plant (2 employees), Group companies (7 employees)
- Second-year training: Nihongi Plant (3 employees), Takaoka Plant (12 employees), Group companies (2 employees)
- Third-year training: Nihongi Plant (5 employees), Takaoka Plant (13 employees), Research & Innovation Center (1 employee), Group companies (8 employees)
- Fifth-year training: Nihongi Plant (9 employees), Takaoka Plant (16 employees), Mizushima Plant (3 employees), Group companies (1 employee)
- Tenth-year training: Nihongi Plant (1 employee), Takaoka Plant (12 employees)
- Fifteenth-year training: Takaoka Plant (6 employees), Group companies (1 employee)
- Worksite training: Takaoka Plant (16 employees*), Research & Innovation Center (10 employees)
- Partner company training: Group companies (115 employees)
- Total: Nihongi Plant (21 employees), Takaoka Plant (67 employees), Mizushima Plant (5 employees), Research & Innovation Center (11 employees), Group companies (134 employees)
- * For employees in their twentieth year and above.
Main training programs for safety
- Safety training: Special safety education for oxygen deficiency, concrete methods related to the four safety cycles, how to handle steam, operation of forklifts, how to handle organic solvents, experience with solvent combustion explosions due to static electricity, experience with exposure to liquid chemicals, and how to handle breathing equipment
- Maintenance / instrumentation training: Machine maintenance, how to read engineering flow designs (EFD), electricity, instrumentation / measuring, and how to handle electric tools
- Field work training: How to use tools / instruments correctly, installation / removal of flanges, testing airtightness of pipes, and plumbing assembly / removal
- Practical safety education: Simulation of hazards associated with working at heights, slinging work, rotating machines, and electricity, and education associated with working in tanks, VR experiences (working at heights and with stepladders, etc.), operating drones, and more
Objective of the session
To acquire basic knowledge and learn about basic machine structure to improve safety awareness.
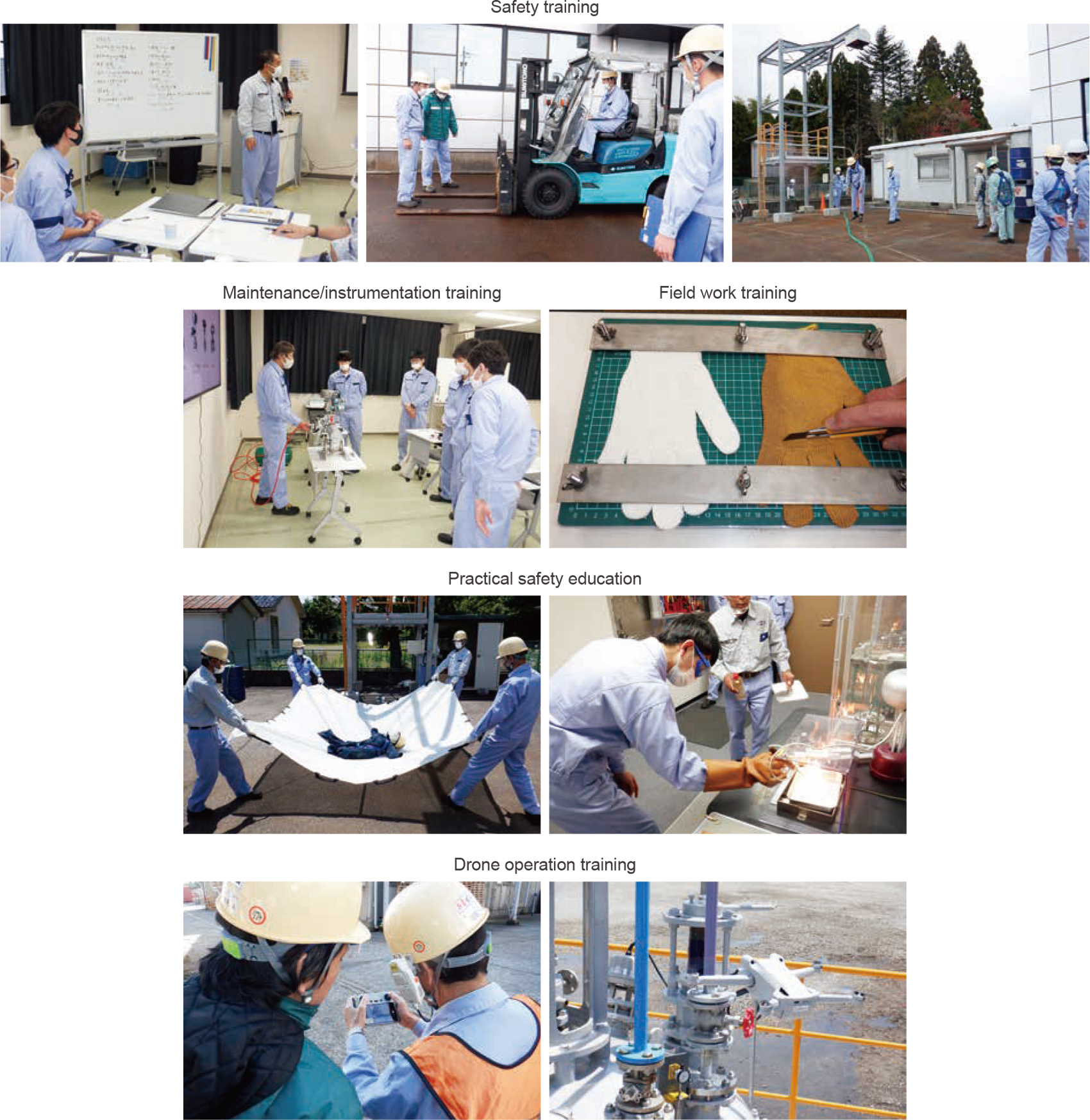