Process Safety and
Disaster Prevention / BCP
At the Nippon Soda Group, recognizing that the continuation of safe, stable production activities and the stable supply of products and services is fundamental to our business activities, we promote process safety and disaster prevention activities. Furthermore, we are constantly working to improve our business continuity plan so that we can quickly recover and restart production activities in the event of a natural disaster or other emergency, and at the same time reinforcing our stable supply structure.
- Regular inspections, repair and renewal of equipment and training of operators at each manufacturing site.
- Improvement of the risk management system through emergency drills and education to prepare employees for possible accidents and disasters.
- Safety reviews by internal experts to verify safety when facilities are constructed or renovated. Regular diagnoses of disaster prevention capabilities by external specialists.
- Regular reviews and improvement of the business continuity plan (BCP), which is designed to ensure preparedness for natural disasters such as large-scale earthquakes and other emergencies that could result in extensive damage.
FY 2024 targets and achievements levels (KPIs)
(Achievement levels ◎:≥ 90% ○:80–90% △:60–80% ×: ≤ 60%) Red text: KPIs
Process Safety and
Disaster Prevention
Risk Management
Risk assessment of process safety and disaster prevention | We conduct risk assessments related to safety and disaster prevention for facilities, machines and manufacturing processes. Identified risks are prioritized and, accordingly, measures to ensure the safety of facilities are implemented and inspections are conducted in sequence. |
---|---|
Establishment of an emergency risk management system | We give the highest priority to preventing accidents and disasters. On the other hand, to prepare for accidents and disasters, we have established an emergency risk management system and conduct periodic drills and exercises to maintain the system in a sound condition. |
Standards on Emergency Response | The Standards on Emergency Response have been developed to ensure prompt and appropriate communication, response, and instruction in the event of a disaster or accident, and their effectiveness is reviewed and revised periodically, and confirmed through training. |
Third-party diagnoses of disaster prevention capabilities
Sompo Risk Management Inc. regularly diagnoses the disaster prevention capabilities of Nippon Soda and its manufacturing Group companies.
In FY 2024, our Nihongi Plant, Takaoka Plant, Mizushima Plant, Chiba Plant and two Group company plants underwent diagnoses.
Safety Management
Safety audit to confirm the safety of plants
To ensure the safety of processes in the construction and renovation of facilities, Nippon Soda Group managers and internal experts conduct safety reviews and audits for facilities and operations in terms of safety, work environment, quality and other factors.
Facilities of Group manufacturing companies undergo periodic Responsible Care (RC) audits to assess the management conditions of manufacturing facilities and these results have been incorporated into activities to improve process safety and disaster prevention.
Safety audits prior to trial operation by the Head Office
Chiba Plant, July 25, 2023
Safety audits prior to trial operation of manufacturing equipment following Phase I of work to increase production capacity of VP polymer solution.
As a result of document and on-site audits, 15 safety issues were identified. After implementing countermeasures for all of these safety issues, trial operation was complete.
Education and Drills for Disaster Prevention
Nippon Soda provides a variety of process safety and disaster prevention training for employees to acquire the knowledge and skills to ensure their safety. We will continue to promote safety and disaster prevention activities with the aim of further improving our safety and disaster prevention activities to achieve the target of “no major accidents at facilities.”
Manufacturing training programs (NTTC: Nisso Technical Training Center)
Each worksite and department conducts continuous education and training in accordance with the CSR action plan. Furthermore, for new employees assigned to our manufacturing sites, we provide manufacturing training programs as a form of new employee training. These programs include experiential education and training related to safety and basic work practices. Moreover, in addition to among new employees, we are also working to improve safety awareness by extending our educational programs to employees in various other positions.
- First-year training: Nihongi Plant (3 employees), Takaoka Plant (8 employees), Mizushima Plant (2 employees), Group companies (7 employees)
- Second-year training: Nihongi Plant (3 employees), Takaoka Plant (12 employees), Group companies (2 employees)
- Third-year training: Nihongi Plant (5 employees), Takaoka Plant (13 employees), Research & Innovation Center (1 employee), Group companies (8 employees)
- Fifth-year training: Nihongi Plant (9 employees), Takaoka Plant (16 employees), Mizushima Plant (3 employees), Group companies (1 employee)
- Tenth-year training: Nihongi Plant (1 employee), Takaoka Plant (12 employees)
- Fifteenth-year training: Takaoka Plant (6 employees), Group companies (1 employee)
- Worksite training: Takaoka Plant (16 employees*), Research & Innovation Center (10 employees)
- Partner company training: Group companies (115 employees)
- Total: Nihongi Plant (21 employees), Takaoka Plant (67 employees), Mizushima Plant (5 employees), Research & Innovation Center (11 employees), Group companies (134 employees)
- * For employees in their twentieth year and above.
Disaster prevention system working in cooperation with local communities
Each Nippon Soda site implements regular disaster drills, which include drills conducted in cooperation with other nearby plants and local governments. These drills are conducted taking into account the environment and other characteristics unique to each region so that they can be applied in real settings.
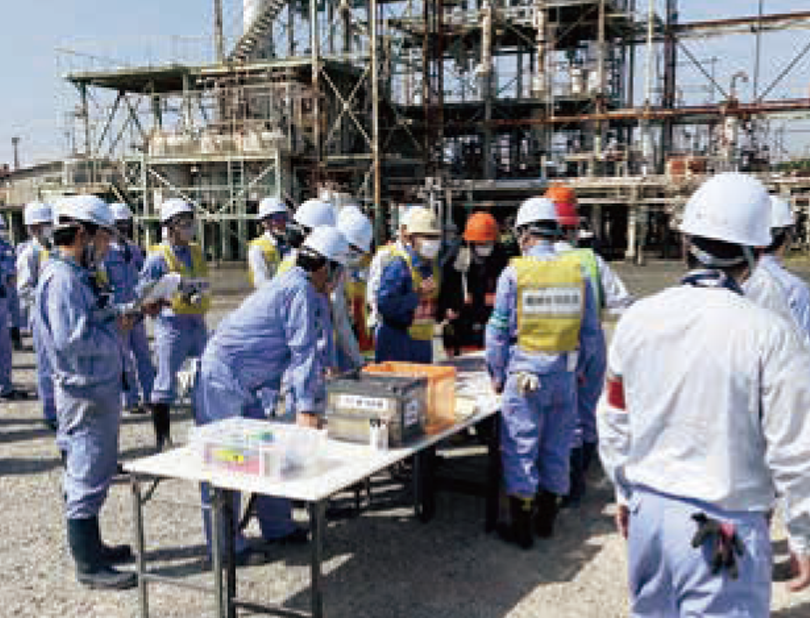
Comprehensive plant disaster drill
(Chiba Plant, May 18, 2023)
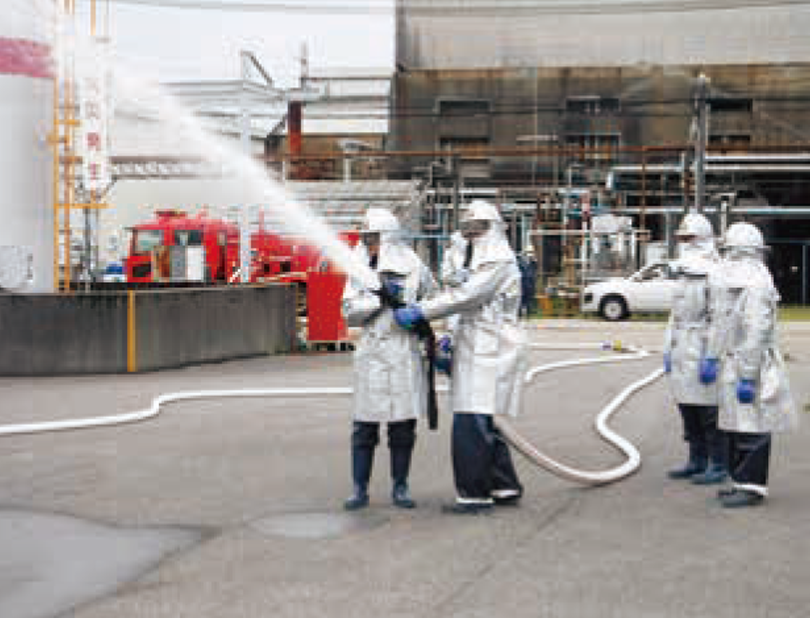
Comprehensive plant disaster drill
(Takaoka Plant, June 6, 2023)
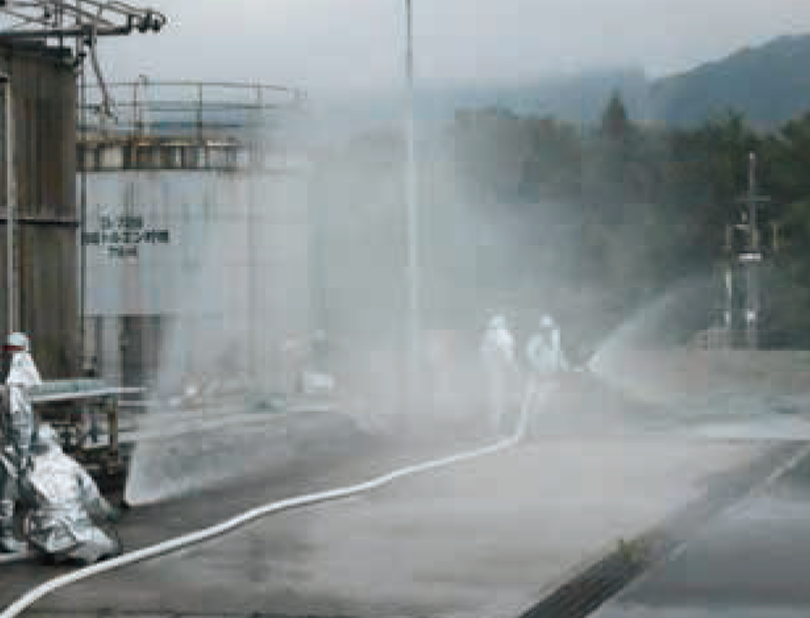
Spring comprehensive plant disaster drill
(Nihongi Plant, June 14, 2023)
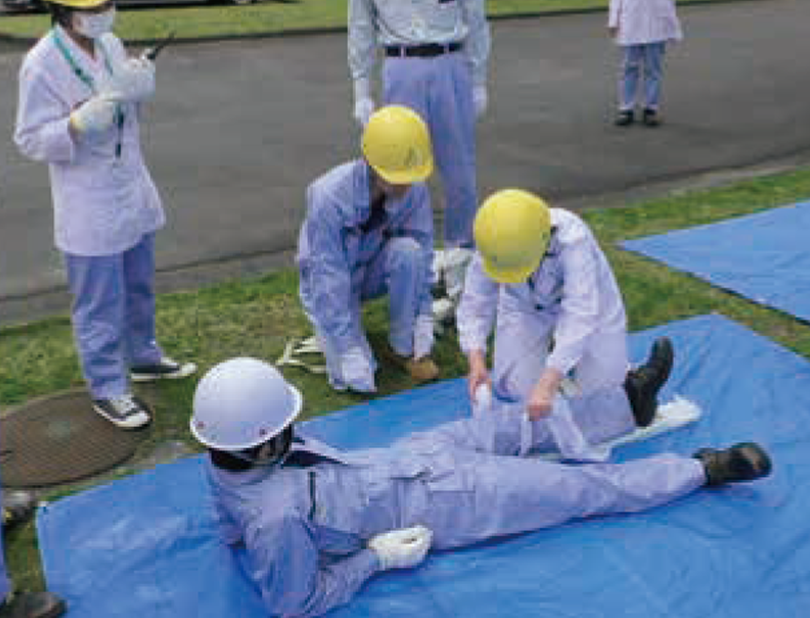
Comprehensive disaster drill
(Odawara Research Center, June 21, 2023)
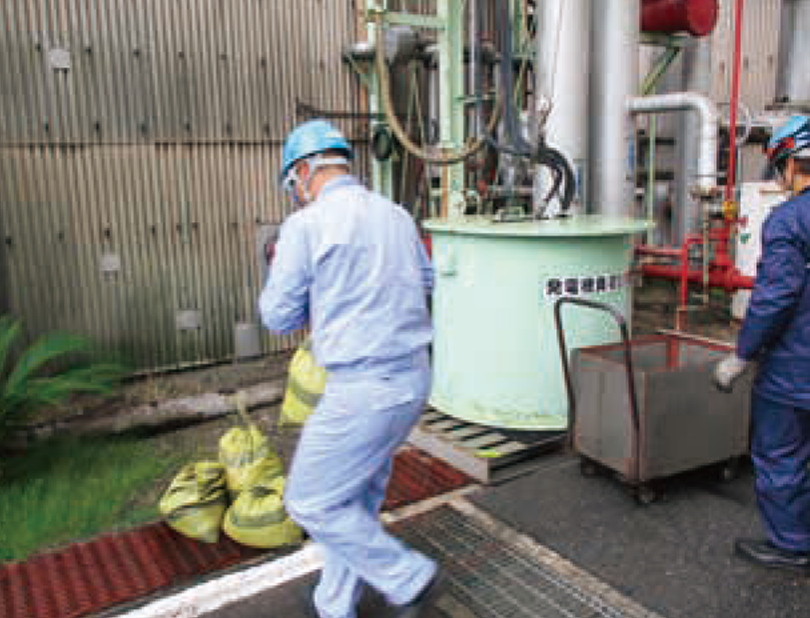
Harmful substance (NaOH) leak response drill
(Mizushima Plant, September 8, 2023)
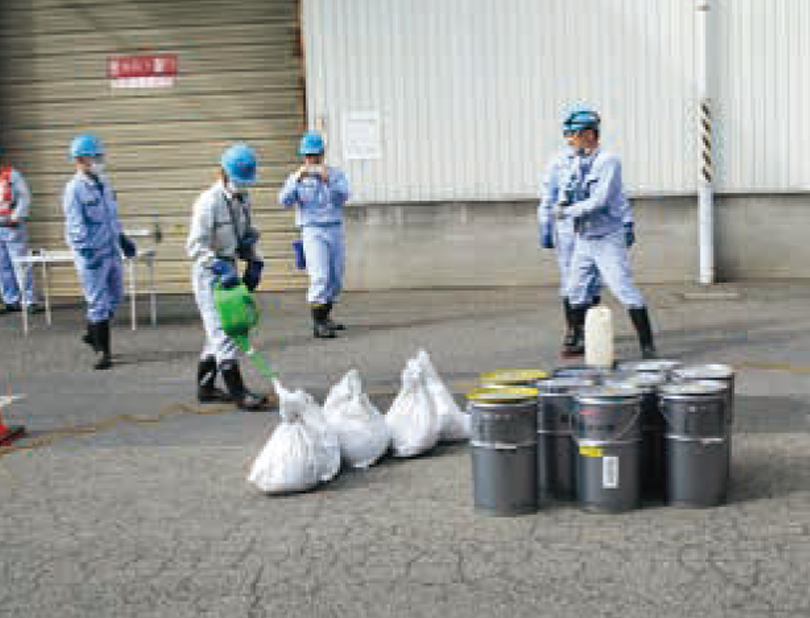
Joint training on response to accidents during product transportation
(Mizushima Plant, September 26, 2023)
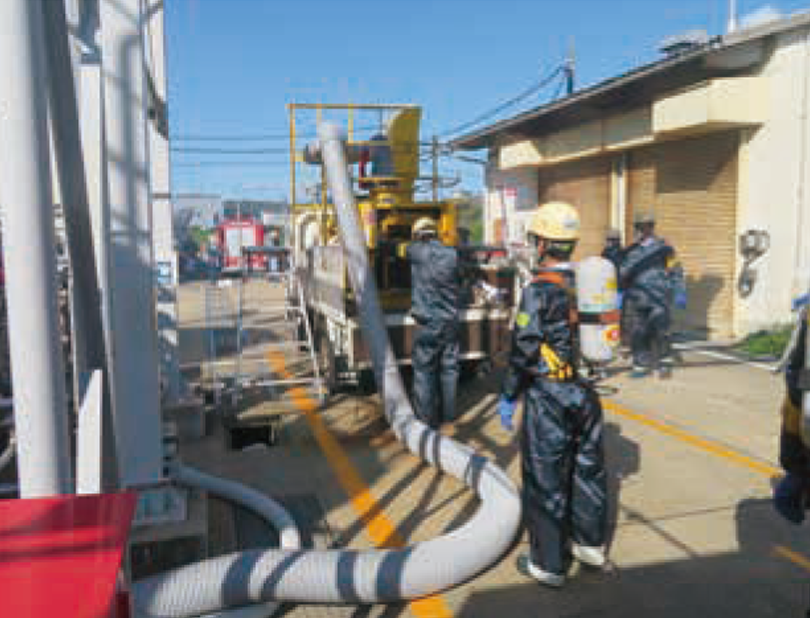
Environmental abnormality response drill
(Takaoka Plant, October 17, 2023)
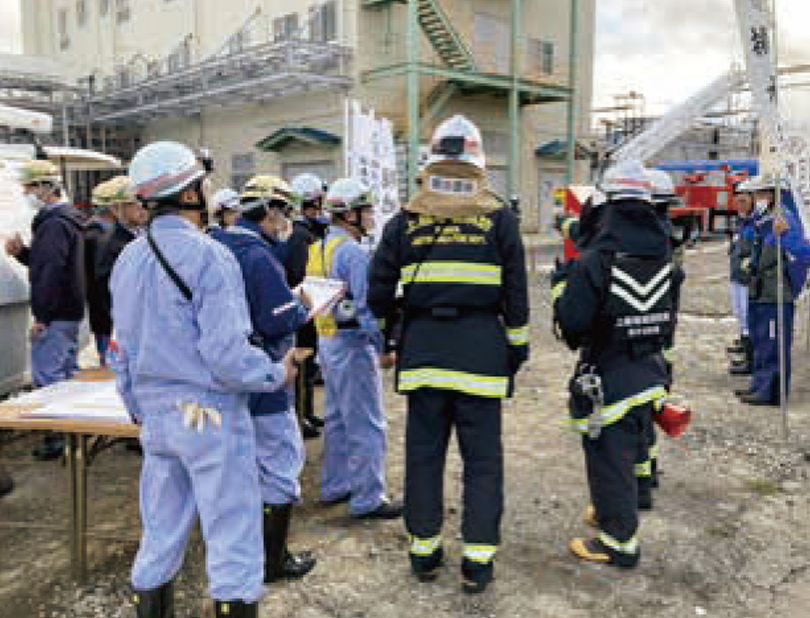
Autumn comprehensive plant disaster drill
(Nihongi Plant, November 14, 2023)
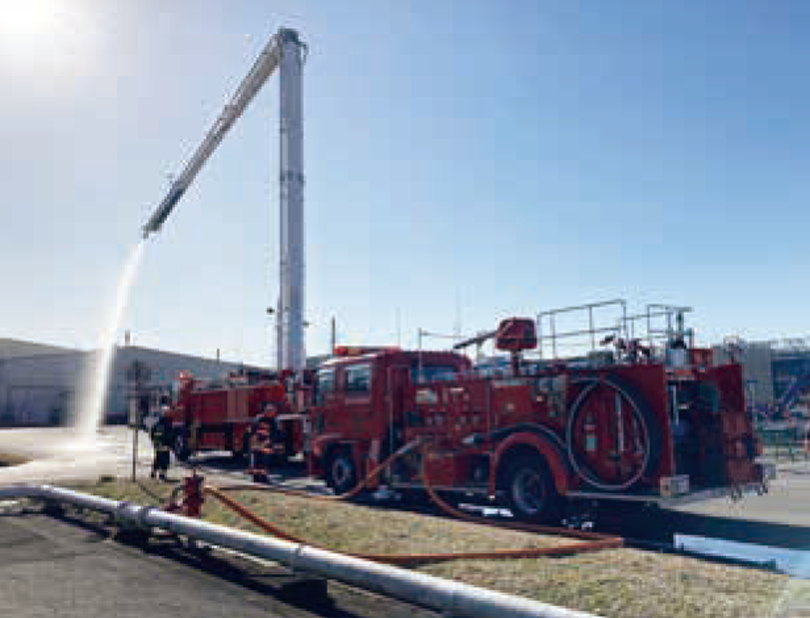
Comprehensive plant disaster drill
(Chiba Plant, February 7, 2024)
FY 2024 Emergency Drills
- * Emergency contact drills (using Otsutae-kun) and comprehensive disaster drills at the Odawara Research Center are conducted jointly with the Chiba Plant.
Business Continuity Plan (BCP)
Basic concept of the BCP
In the event of a natural disaster such as a large-scale earthquake or other crisis that can result in serious damage to Nippon Soda worksites, our social responsibility is to ensure the safety of local residents, full-time and temporary employees and partner company employees. Based on this concept, the principles of the BCP are defined as follows:
- 1.The highest priority is placed on checking the status and ensuring the safety of Nippon Soda’s own employees, partner company employees and temporary employees and their families, and ensuring the safety of residents in communities where the Company’s business sites are located.
- 2.The consciousness of serving the public and community is shared among all personnel throughout the Company.
- 3.Efforts are focused on protecting the safety of any affected Head Office, plants, research centers, or sales office sites.
- 4.Measures should be taken to establish a system that allows Nippon Soda’s employees, partner company employees and temporary employees who are engaged in ensuring safety and security to act flexibly and at their discretion according to the circumstances.
Continuation of supply of products according to customer needs
The BCP of Nippon Soda aims to ensure, in the event of a natural disaster or other crisis, safety as well as the supply of products to customers as requested. To achieve this objective, improvement is accelerated using the PDCA cycle.
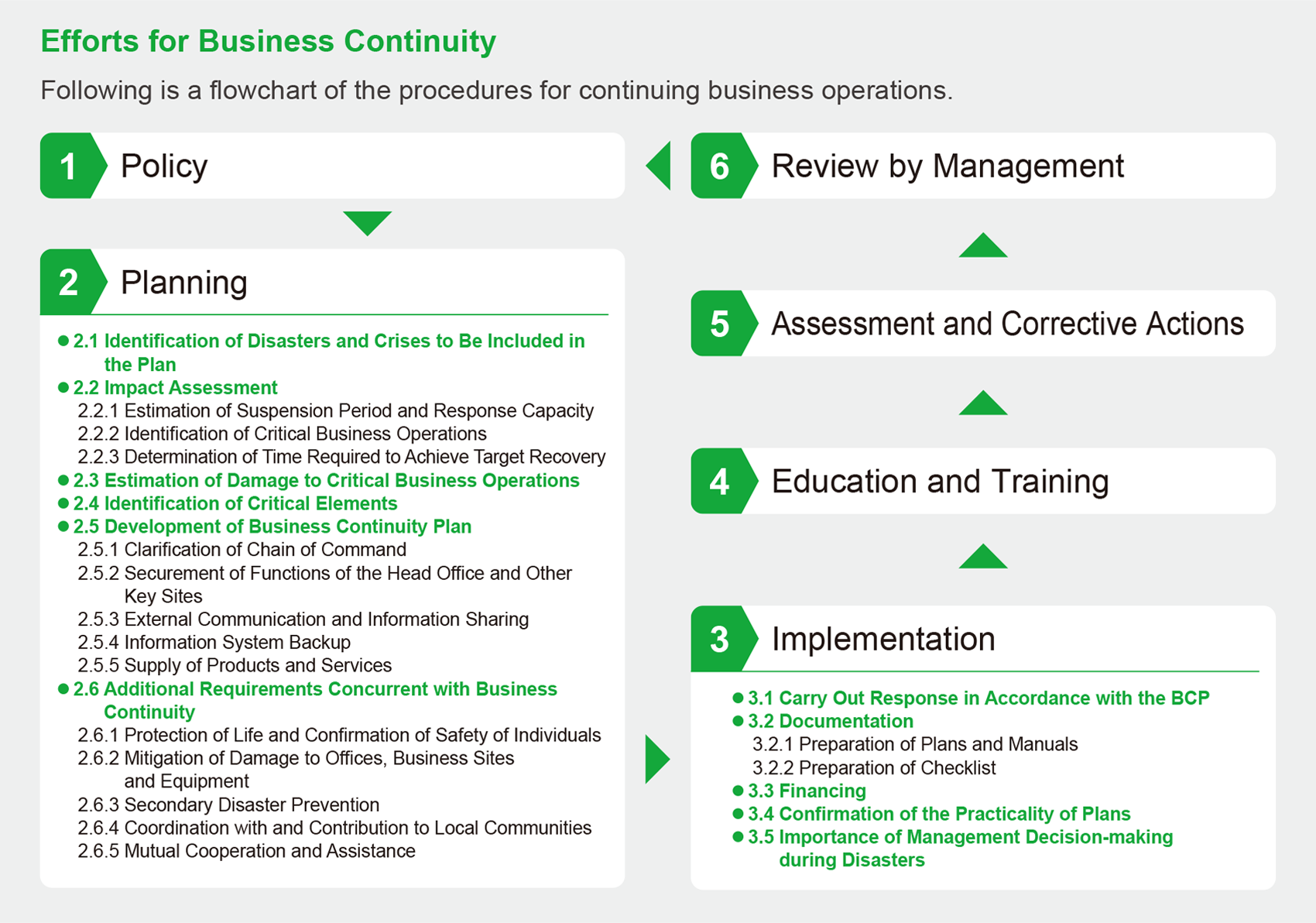
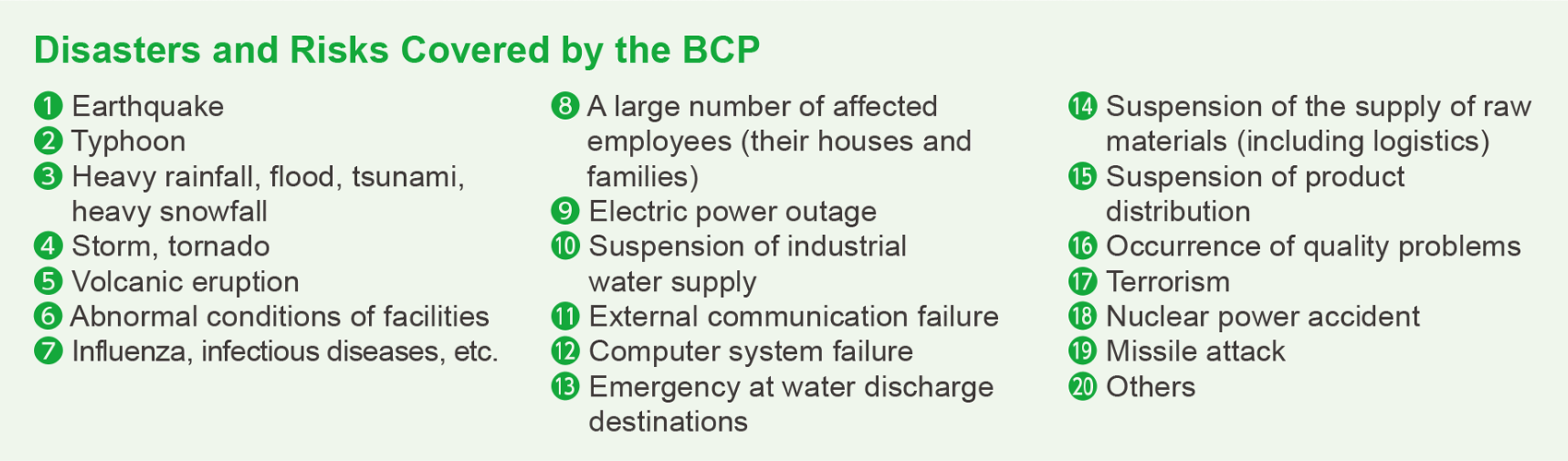
We will continue our efforts to achieve the target of “no major accidents at facilities” through the constant improvement of safety management, risk management, education, disaster prevention drills and other measures. We will also improve and review the BCP in a systematic manner.
- 1.Major accidents at facilities: Target: Zero accidents
- 2.Maintenance and improvement of the BCP Creation
of FY 2025 version of BCP manual (Ver. 14)